Robotics in small manufacturing is changing how businesses operate. These machines help companies work faster and better, making them more competitive. This article explores the journey of robotics in small manufacturing, the benefits they bring, the challenges faced, and what the future holds.
Key Takeaways
Robots have come a long way and are now an important part of small manufacturing.
Using robots can help businesses make more products in less time.
Robots can lower costs by reducing mistakes and waste.
Training workers to use robots is key to success in small manufacturing.
The future of robotics in small manufacturing looks bright with new technologies on the way.
The Evolution of Robotics in Small Manufacturing
Historical Context and Early Adoption
Robotics in manufacturing began to take shape in the 1960s. During this time, the first industrial robots were introduced, marking a significant shift in how factories operated. These early robots were mainly used for repetitive tasks, helping to boost productivity and reduce human error. As industries recognized the benefits, more companies started to adopt these machines, paving the way for a new era in manufacturing.
Technological Advancements Driving Change
Over the years, robotics technology has advanced rapidly, leading to smarter and more efficient robots. Key developments include:
Improved sensors that allow robots to interact better with their environment.
Artificial intelligence integration, enabling robots to learn and adapt.
Enhanced programming tools that make it easier for manufacturers to implement robotic solutions.
These advancements have made robots more accessible and effective for small manufacturers, allowing them to compete in a global market.
Key Milestones in Robotics Integration
Several important milestones have marked the journey of robotics in small manufacturing:
The introduction of the first industrial robot in the 1960s.
The rise of automation in the 1980s, which saw robots becoming commonplace in factories.
The development of collaborative robots, or cobots, in the 2000s, designed to work alongside humans safely.
These milestones highlight the ongoing evolution and increasing importance of robotics in the manufacturing sector.
The robotics journey in manufacturing shows how technology can transform industries, making them more efficient and competitive.
Overall, the evolution of robotics in small manufacturing has been marked by significant changes that have shaped the industry as we know it today. With continued advancements, the future looks promising for small manufacturers willing to embrace these technologies.
Highlight: industrial robots in manufacturing have become more widespread during the automation age.
Benefits of Robotics in Small Manufacturing
Enhancing Production Efficiency
Robotics can significantly boost production efficiency in small manufacturing. By automating repetitive tasks, robots can work faster and more accurately than humans. This leads to higher output, optimized production processes, and less downtime. For example, a robotic arm can assemble parts continuously without needing breaks, which helps meet customer demands more effectively.
Reducing Operational Costs
One of the biggest advantages of using robots is the potential for cost savings. By implementing robotics, small manufacturers can reduce operational costs by up to 30%. Additionally, the implementation of robotics can lead to a significant reduction in maintenance costs, offering savings ranging from 10% to 40%. This reduction comes from lower labor costs, decreased waste, and fewer errors in production. Here’s a quick look at how costs can be saved:
Lower labor costs: Robots can replace some manual jobs.
Less waste: Robots are precise, which means fewer mistakes.
Faster production: More products can be made in less time.
Improving Product Quality
Robots help improve the quality of products by ensuring consistency and precision in the manufacturing industry. They can perform tasks with a level of accuracy that is hard for humans to match. This leads to fewer defects and higher customer satisfaction. Quality control processes can also be enhanced with robotics, as machines can inspect products more thoroughly than a human could.
In summary, the integration of robotics in small manufacturing not only enhances efficiency but also leads to significant cost reductions and improved product quality.
By embracing robotics, small manufacturers can stay competitive in a rapidly changing market.
Benefit | Description |
---|---|
Production Efficiency | Increased output and reduced downtime |
Operational Costs | Savings of up to 30% in costs |
Product Quality | Higher consistency and fewer defects |
Challenges Faced by Small Manufacturers in Adopting Robotics
Financial Constraints and Investment
Many small manufacturers struggle with the financial burden of investing in robotics. High initial costs can deter businesses from making the leap. Here are some common financial challenges:
Limited budgets for new technology
Uncertainty about return on investment (ROI)
Difficulty in securing loans or funding
Workforce Training and Skill Development
Another significant hurdle is the need for proper training. Employees must learn how to work with new robotic systems. This can be a challenge because:
Training programs can be expensive.
There may be a lack of skilled trainers available.
Employees might resist change due to fear of job loss.
Integration with Existing Systems
Integrating a robotics system into current manufacturing processes can be tricky. Compatibility issues often arise, making it hard to blend new technology with old systems. Some integration challenges include:
Outdated machinery that cannot work with new robots
Software compatibility problems
The need for ongoing maintenance and support
Adopting robotics is not just about buying machines; it’s about changing the way a business operates. In summary, small manufacturers face several challenges when adopting robotics, including financial constraints, workforce training needs, and integration issues. Addressing these challenges is crucial for successful implementation and growth in the industry.
Innovative Applications of Robotics in Small Manufacturing
Automation in Assembly Lines
Robots are changing how assembly lines work. They are essential in optimizing material handling processes, utilizing articulated and SCARA robots for tasks like welding, assembly, and packaging. They can do tasks faster and more accurately than humans. This leads to higher production rates and less waste. Here are some key benefits of using robots in assembly:
Increased speed of production
Consistent quality of products
Ability to work in dangerous environments
Robotics in Quality Control
Quality control is crucial in manufacturing. Robots can help check products for defects. They use cameras and sensors to find problems that humans might miss. This ensures that only the best products reach customers. Quality assurance is improved significantly with robotic systems.
Customization and Flexibility in Production
Robots can be programmed to make different products without needing a lot of changes. This flexibility allows small manufacturers to meet customer demands quickly. Robots can adapt to new tasks easily, making them valuable in today’s fast-paced market. Here are some ways robots help with customization:
Quick reprogramming for different tasks
Ability to handle small batch sizes
Enhanced creativity in product design
In the world of small manufacturing, robots are not just tools; they are partners that help businesses grow and adapt to new challenges.
Overall, the use of robotics in small manufacturing is transforming how products are made, ensuring efficiency and quality at every step.
Future Trends in Robotics for Small Manufacturing
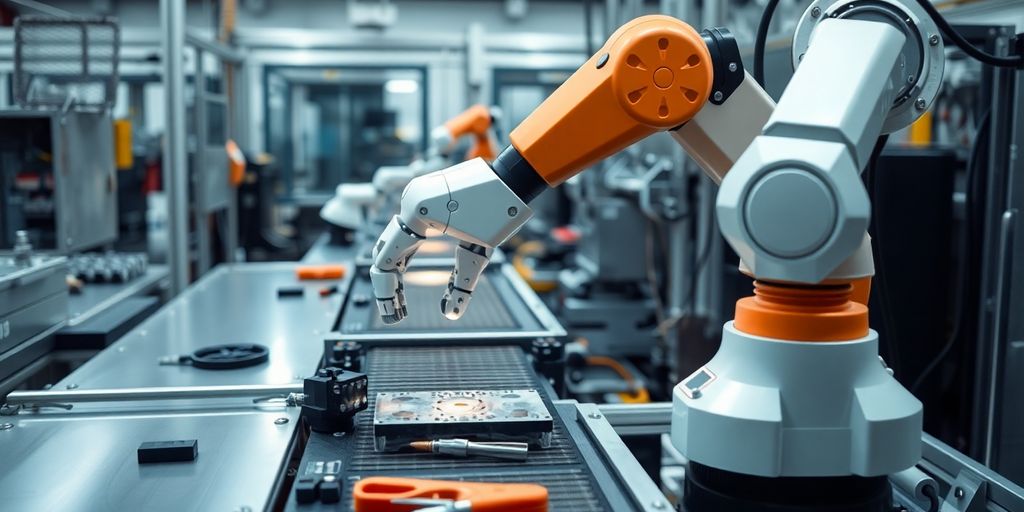
Emerging Technologies and Innovations
The future of robotics in small manufacturing is bright, with many exciting technologies on the horizon. Increased deployment of collaborative robots (cobots) is expected, allowing machines and humans to work side by side safely. These robots are designed to assist workers rather than replace them, making them a great fit for small businesses.
The Role of Artificial Intelligence
Artificial intelligence (AI) is set to play a major role in the evolution of robotics. AI can help robots learn from their environment and improve their performance over time. This means that robots will become more efficient and capable of handling complex tasks. Here are some key points about AI in robotics:
Enhanced decision-making: Robots can analyze data and make better choices.
Predictive maintenance: AI can help predict when machines need repairs, reducing downtime.
Personalization: Robots can adapt to specific production needs, making them more versatile.
Sustainability and Eco-friendly Practices
As the world becomes more focused on sustainability, robotics will also adapt. Small manufacturers are looking for ways to reduce waste and energy use. Eco-friendly practices in robotics can lead to a cleaner environment and lower costs. Some trends include:
Using energy-efficient robots.
Recycling materials in production.
Implementing processes that minimize waste.
The integration of robotics in small manufacturing is not just about efficiency; it’s also about creating a sustainable future for our planet.
In summary, the future of robotics in small manufacturing will be shaped by emerging technologies, the integration of AI, and a strong focus on sustainability. These trends will help small businesses thrive in a competitive market while also being responsible stewards of the environment.
Case Studies: Success Stories of Robotics in Small Manufacturing
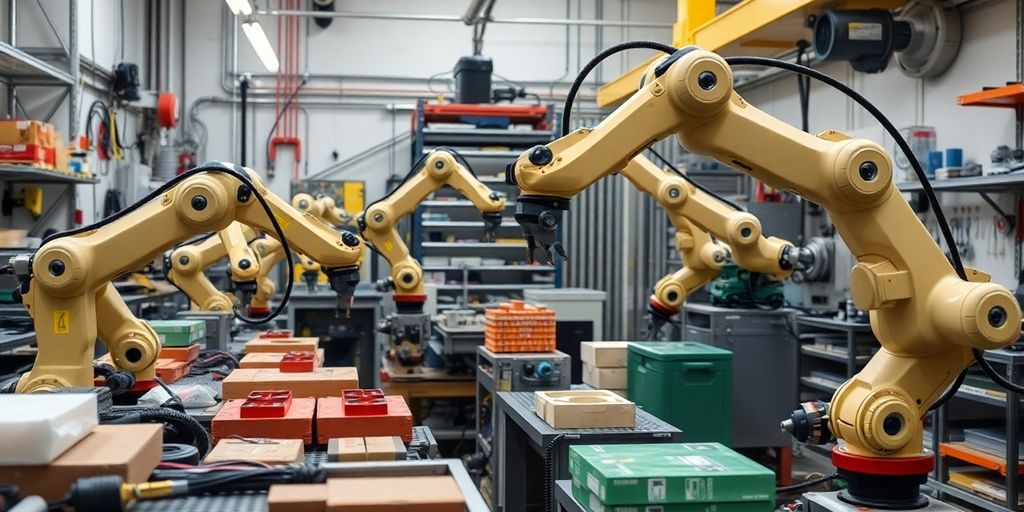
Transformative Impact on Local Businesses
Many small manufacturers have seen a huge boost in their operations thanks to robotics. For instance, a local bakery implemented robotic arms for packaging, which allowed them to increase their output by 30%.
Lessons Learned from Early Adopters
Early adopters of robotics have shared valuable insights:
Start small and scale up gradually.
Invest in training for your team.
Choose technology that fits your specific needs.
Scalability and Growth Opportunities
Robotics not only helps in current operations but also opens doors for future growth. Companies that embraced robotics reported:
Increased production capacity.
Ability to take on larger orders.
Improved customer satisfaction due to faster delivery times.
Adopting robotics can be a game-changer for small manufacturers, leading to better efficiency and growth.
Company Name | Robotics Used | Efficiency Increase |
---|---|---|
Local Bakery | Robotic Arms | 30% |
Furniture Co | Automated Assembly | 25% |
Tech Startup | Robotic Process Automation | 40% |
These real-world examples show how robotics can transform small manufacturing businesses, making them more competitive and efficient.
Collaborative Robotics: Enhancing Human-Machine Interaction
Safety and Efficiency in Collaborative Workspaces
Collaborative robots, or cobots, are designed to work alongside humans in a safe and efficient manner. They help reduce the risk of accidents while boosting productivity. Recent studies show that cobots can significantly improve flexibility in manufacturing processes. Here are some key benefits of using cobots:
Increased safety for workers
Enhanced productivity
Greater adaptability to different tasks
Human-Centric Design in Robotics
The design of collaborative robots focuses on making them easy to use for people. This means they are often lightweight and can be programmed without needing advanced technical skills. The goal is to create a user-friendly experience that encourages workers to embrace this technology. Some important features include:
Simple interfaces for easy operation
Adjustable settings for various tasks
Intuitive controls that require minimal training
Building a Synergistic Workforce
The combination of human workers’ skills and robotic efficiency creates a powerful team. By working together, humans and robots can achieve more than either could alone. This partnership leads to:
Improved job satisfaction for workers
Higher quality products
Faster production times
Collaborative robotics is not just about machines; it’s about creating a better work environment for everyone involved. In summary, the integration of collaborative robots in manufacturing is transforming how we work. They enhance safety, improve efficiency, and create a more engaging workplace for employees. As we continue to explore the potential of cobots, their role in the future of manufacturing looks promising.
Conclusion
In summary, robotics are changing the way small manufacturing businesses operate. By using robots, these companies can work faster and make fewer mistakes. This not only helps them save money but also allows them to produce better products. As technology keeps improving, we can expect to see even more robots in factories. This shift will help small manufacturers stay competitive and meet the needs of their customers. Overall, embracing robotics is a smart move for small businesses looking to grow and succeed in today’s market.
Frequently Asked Questions
What are the main benefits of using robots in small manufacturing?
Robots help small manufacturers work faster, save money, and make better products. They can do tasks quickly and accurately, which means less waste and more profit.
How can small manufacturers afford robots?
While robots can be expensive, many companies offer financing options, and there are grants available. Small manufacturers can also start with one robot and gradually add more as they see the benefits.
Do workers need special training to work with robots?
Yes, workers may need some training to operate and maintain robots. However, many robots are designed to be user-friendly, so training can be quick and easy.
Can robots work alongside humans?
Absolutely! Many robots are designed to work alongside people. This helps make jobs safer and allows humans to focus on more complex tasks.
What are some common types of robots used in small manufacturing?
Common robots include robotic arms for assembly, mobile robots for moving materials, and inspection robots for quality control. Each type has a specific job that helps improve the overall process.
What does the future hold for robotics in small manufacturing?
The future looks bright! We can expect more advanced robots that are smarter and more efficient, with new technology like artificial intelligence making them even better at their jobs.